Use of an electro-sorption cell to remove trivalent chromium
Por: E. T. Jasso Olmedoa; A. Ramírez Padillab; A. C. Gaytán Larab; J. C. Martínez Barróna; I. López Báeza; J. C. Baltazar Veraa and L. G. Alvarado Montalvoa
Abstract
A large number of metallurgical-mining operations involve the use of water as part of their processes, and as a consequence, the generation of effluents containing metal ions, which, being present in concentrations of parts per million represent a certain difficulty for the treatment and the recovery of the metallic species. In the present work the treatment of a synthetic solution of 100 ppm Cr(III) is approached by means of a laboratory scale cell using activated carbon electrodes supported in graphite to effect a separation by electro-sorption. Adsorption tests of activated carbon were performed, finding a low capacity to adsorb Cr(III); these results were contrasted against the electro-sorption process, in which an obvious advantage was compared with respect to traditional adsorption, by increasing the removal beyond double with respect to adsorption results.
Introduction
Both in the mining industry, and others whose processes are related to the use of metals, one of the problems that arise, is that during the processing and/or recovery of the element of interest, there are water effluents with metallic content, which in the cases of arsenic, cadmium, chromium, lead and selenium, mainly, represent a potential danger when exposed to bodies of water, since their interaction with the environment represents a potential adverse impact to it [1]. Hence, over time, various techniques, strategies and even processes have been developed, whose purpose is to minimize the impact that such effluents can cause. In this sense, one of the most popular is chemical precipitation, which aims to transfer the contaminant to a solid state, so that it can then be filtered, separated from the effluent and treated, now generating a solid residue [2]. One of the main problems that this type of strategies represents is the fact that the metallic content is relatively low, that is why it is considered a contaminant, and that the development of a process involves the manipulation of large volumes of solution. In this sense, other separation techniques have been developed, trying to reduce the volume where the contaminant is, such is the case of reverse osmosis, adsorption, ion exchange, electro dialysis and electrodeionization mainly, whose advantage lies in being able to operate continuous systems or semi-continuous and be feasible to operate before large volumes of solution to be treated [3]. Some of the disadvantages that these systems could offer would be: the generation of high pressures within the system, the depletion of adsorbent or exchanger, fouling of membranes and high operational costs, to name a few. In this sense, a technology based on an adsorption system has been developed for not a long time, where an external electric field is applied: capacitive deionization, CDI. This technique is based on the application of a low electric field: about 1.0 V, which induces the electrical adsorption of ions to each of the respective electrodes, where electrodes are used that offer a high surface area, capable of supporting the adsorption of as many ions as possible [4-6]. Once the dispossession of the ions is achieved, the field is interrupted or the field is reversed to desorb them. The challenge in this kind of systems is to find the best electrode material and the operational parameters [7-10].
In this work, tests of trivalent chromium electro-sorption are performed on an activated carbon surface supported on graphite, in such a way that a greater surface area is offered to perform the separation, in addition to adsorption tests of the same species on activated carbon commercial.
Experimental
Preparation of solutions
Cr(III) solutions were prepared at 100 ppm from CrCl3 6H2O (Baker Analyzed® 99.1% purity) and deionized water (18M), commercial coconut shell activated carbon were employed, a multi-stirrer plate was used to stir the samples at 400 rpm, using stirring bars of a half of inch and 25 mL Erlenmeyer flasks. The concentration of chromium was obtained from Atomic Absorption Analysis (Analyst 200 Perkin Elmer).
Carbon dosification
To know the effect of the mass of activated carbon, an adsorption experiment was performed using 25 mL Erlenmeyer flasks, where the following quantities of activated carbon were evaluated and shaken in contact with 20 mL of Cr(III) solution over a period of 24 hours: 20, 38.4, 58.9, 103, 150, 202 and 301 mg. After this time the solution was filtered and the chromium concentration was determined.
Kinetics
To assess the rate at which adsorption was carried out, a kinetics was run in a volume of 25 mL of trivalent chromium solution, with 300 mg of activated carbon, at a constant stirring of 400 rpm. This system was repeated for different times, in order to evaluate adsorption within 2.5 hours.
Electro-sorption
Electrochemical system. As is showed at Figure 1, electro-sorption cell was conformed by 2 acrylic plates that contained a graphite electrode (7.5 x 4 cm), each one, and one acrylic plate of 6 mm of thickness and electrode area opened, through which 500 mL of the test solution was recirculated at 10 mL min-1, using a peristaltic pump: Cole-palmer 6-600 rpm, 7553-20, and L/S master flex® tubing. The external electric field was applied using a GW-Instek power supply.
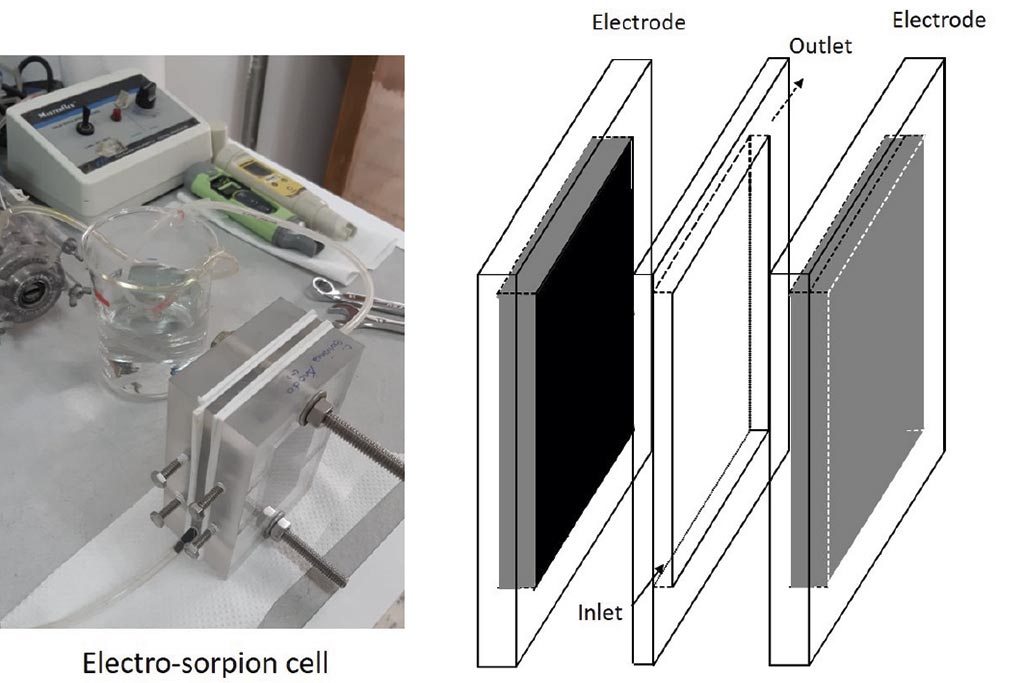
Electrode preparation. The graphite electrodes on plate were subjected to a constant weight, moisture free procedure; then several layers of a mixture of Nafion® solution and activated carbon were applied to a uniform surface. They were then dried in an oven for 30 minutes at 70 °C. The weight of added activated carbon was approx. 1 gram in each electrode.
Results
Carbon dosification
Figure 2 shows the results of the activated carbon dosing experiment for a conventional adsorption system. As can be seen, the change in mass related to carbon removal is representative, achieving a concentration of about 2 ppm when using 300 mg of the substrate, which represents an elimination of 8 mg of trivalent chromium per gram of carbon activated used in a 24 hour period. The removal is proportional to the mass used. According with these results, 300 mg were selected as dosage to be used in the following experiments. On other hand at Figure 3, can be observed that the pH were increased as mass of activated carbon was used, it mean that the species are changing, and it is important to remember that in the case of trivalent chromium, around 6.2, the specie is a precipitate.
On other hand, when the data are treated, the concentrations in the equilibrium can be obtained, Figure 4. That graph shows how the concentration in the solid phase, qe, is each time bigger, to reach a concentration in the liquid phase, Ce, of 3 ppm. And since that point the concentration in the solid phase go down. That shows a low capacity to adsorb ions, just 9 mg of Cr(III) per gram of solid, and only selective to so low concentrations.
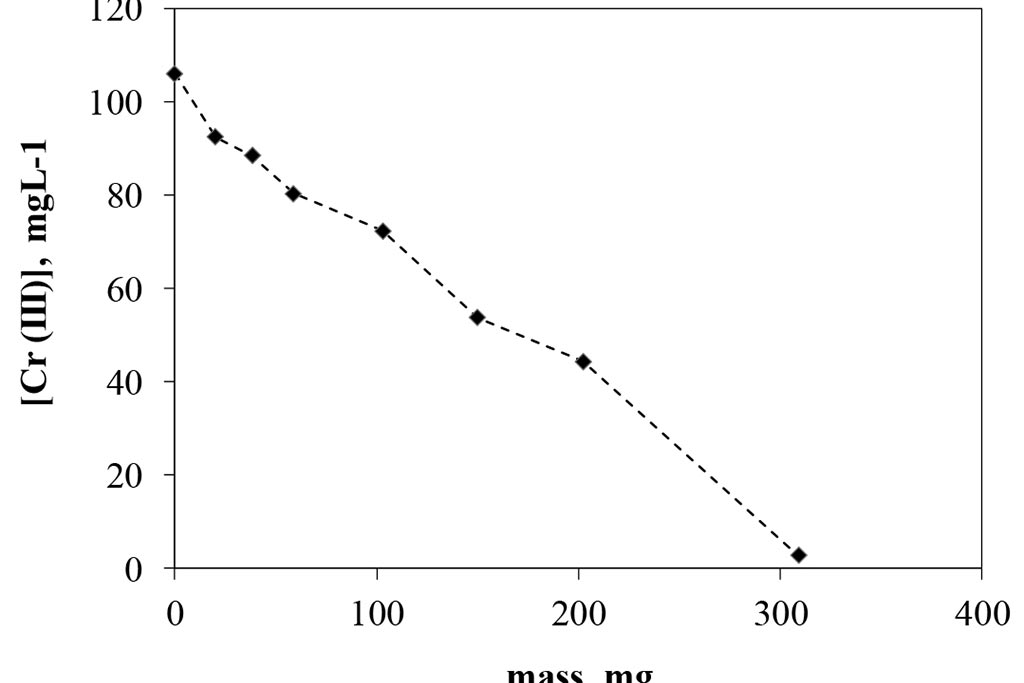
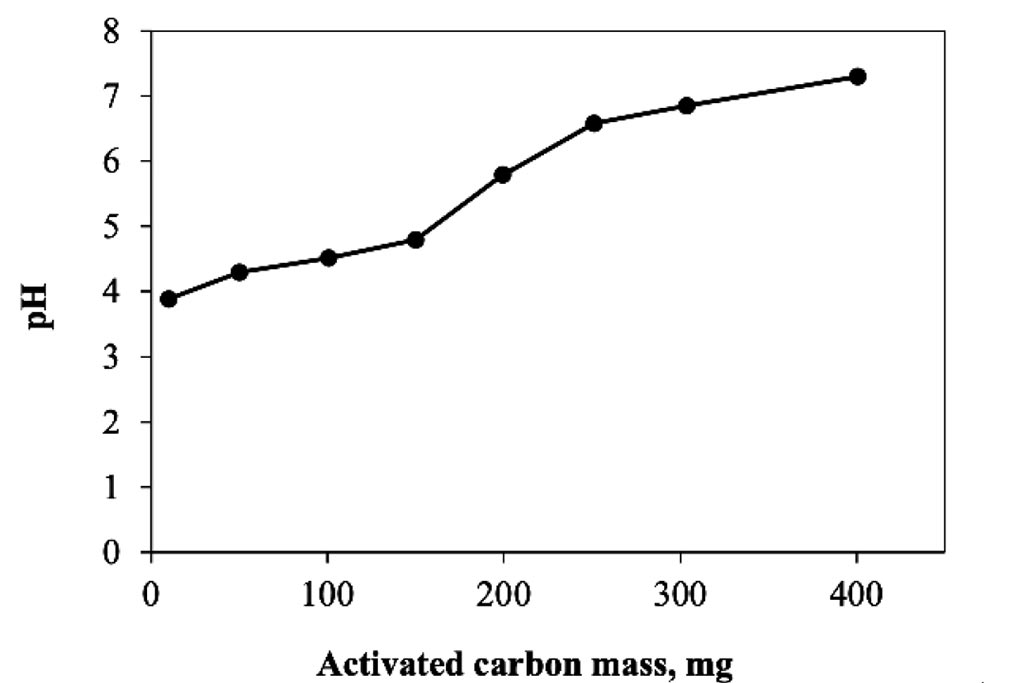
Kinetics
For its part, in Figure 5, the changes of chromium concentration were monitored at different times. How it can be seen that the most important changes occur during the first minute, where 44 ppm, equivalent to 1 mg of chromium per minute, or 44 ppm min-1 were removed. Subsequently, between the minute 1 and 30, was a decreasing at ratio 30 ppm min-1, after this first half of hour the rate decreased in a ratio of 18.25 ppm min-1, and
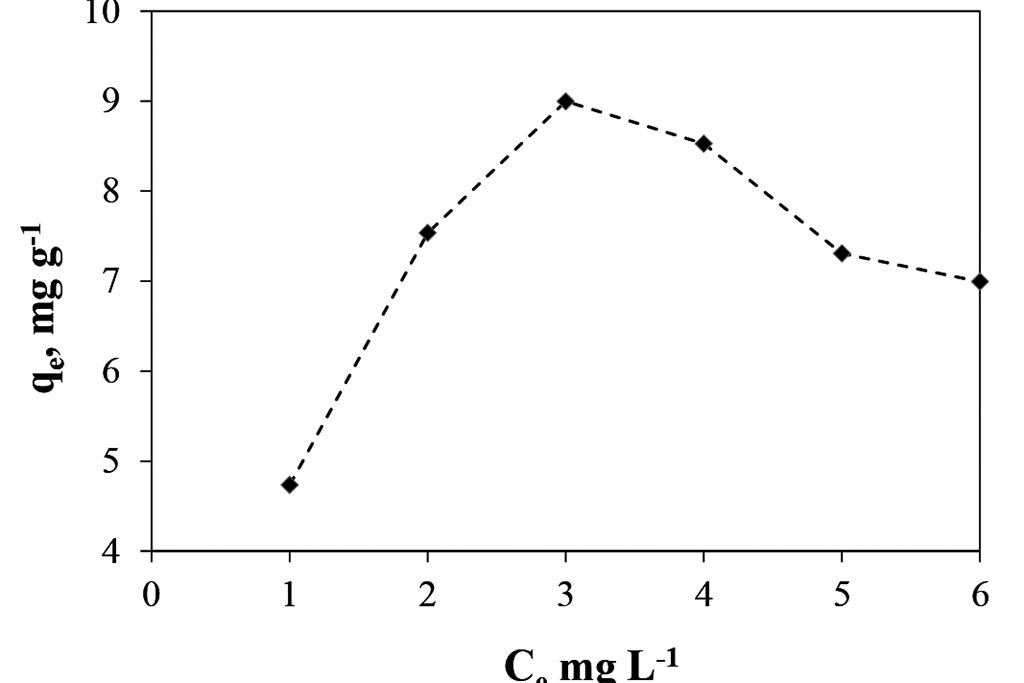
finally, after the 1.3 h, the rate go down to 2.6 ppm min-1. In a half of hour the system reaches a concentration of approximately 25 ppm and from there continue decreasing until reaching a concentration of 2 ppm in a span of 2.5 hours. This indicates the system that is capable of removing approx. 7.65 mg of trivalent chromium per gram of activated carbon used in 2.5 hours.
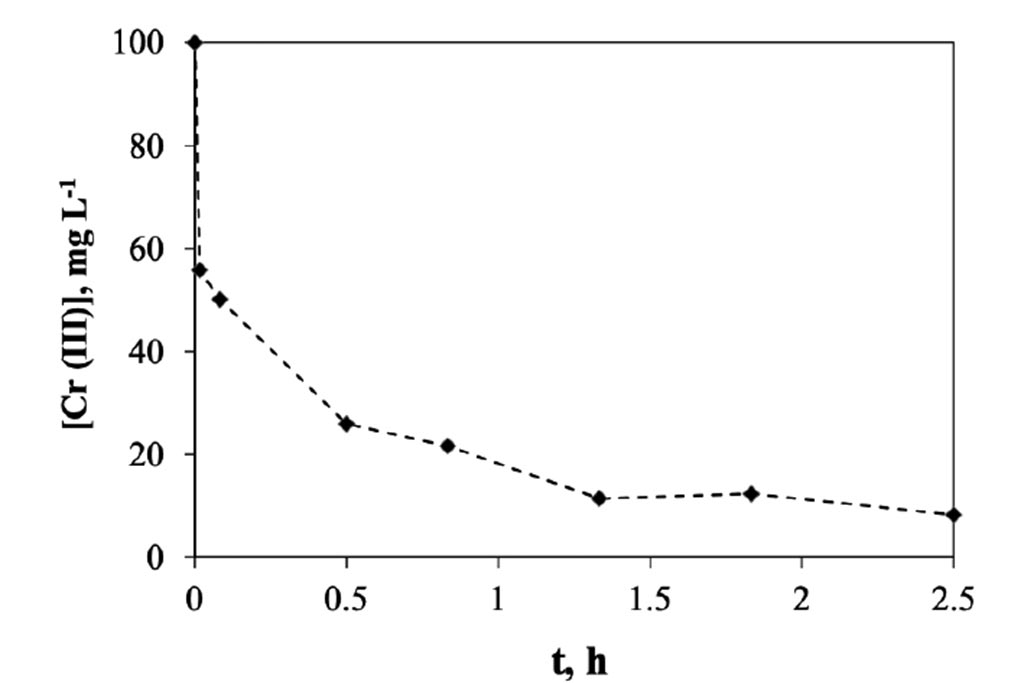
Electrosorption
When the electro-sorption system is used, it was found that the changes are more gradual, Figure 6, because it is a semi-continuous system, in contrast to the previous one, of adsorption, where it is a totally type system batch. In this other system, on the other hand, each time the solution passes through the cell returns to the original container, mixing with the solution remaining in the system, which is why the changes are smaller. However, we can see enough 30 minutes in the cell to achieve maximum removal, which when transferred to calculations represents a removal of 8.0 mg of trivalent chromium per gram of carbon used in the cell. This information indicates that it is capable of eliminating trivalent chromium mass more quickly than in a conventional batch system. The higher rate happens during the first 10 minutes, in a ratio of approx. 1.2 ppm min-1, but that represents 0.5 mg per minute, after this time, in the next 20 minutes the rate go down, 0.18 ppm min-1 and finally, after the first half of hour the rate is constant in a value of 0.0125 ppm min-1. The pH values were monitored during the experiment, Figure 7, and how is possible to see, this started in a pH of 4 and finished at 5.5. Which means that not precipitation occurred during the experiment. On other hand in the Figure 8, the conductivity of the solution behavior is presented, and how can be appreciated, those values tends go down as that is expected.
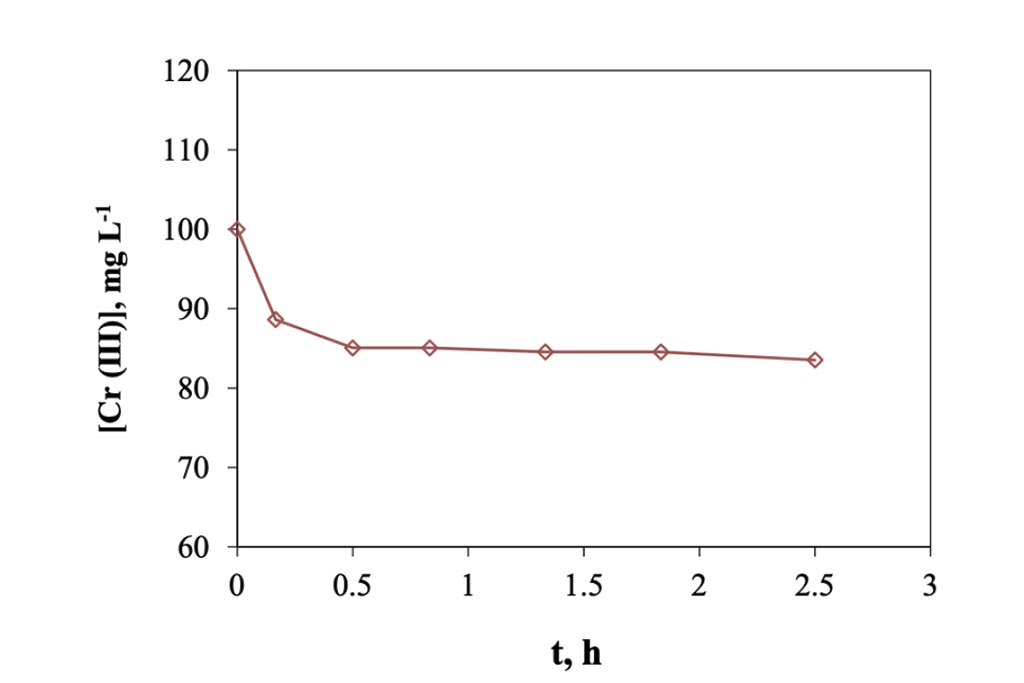
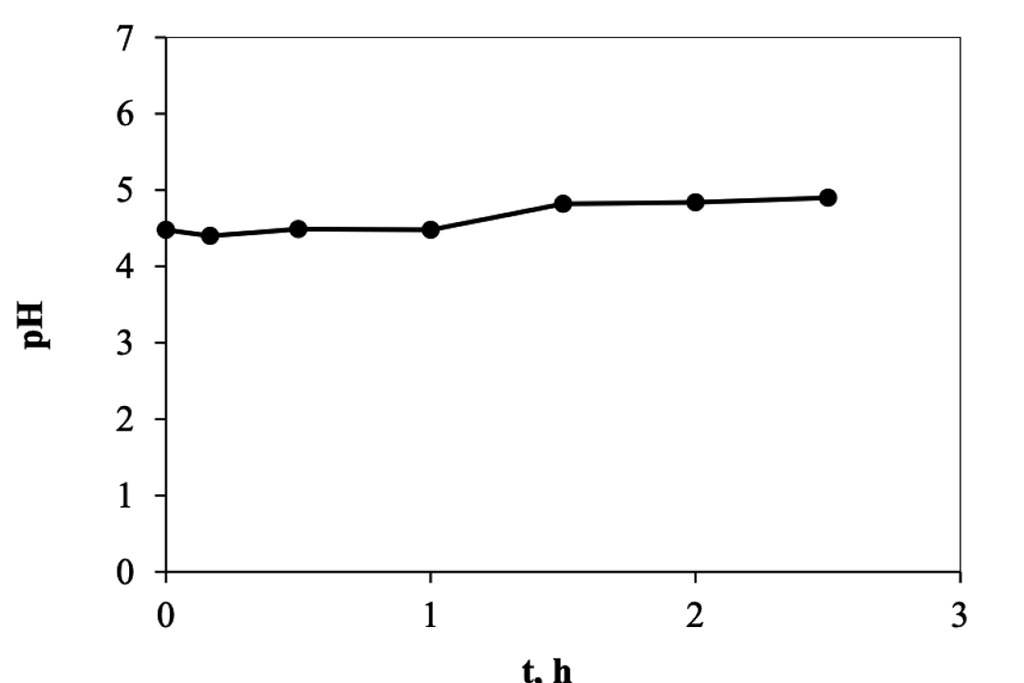
Conclusions
According to the results obtained, it is determined that it is more feasible to eliminate trivalent chromium ions by electro-sorption, because the times in which it is achieved are dramatically reduced, compared to a conventional adsorption system, with the advantage of being able to perform it reversibly, however, a continuous system should be used to visualize results in which the concentration declines in a more dramatic way, which implies the use of a larger mass of the adsorbent substrate. It is highly recommended to study
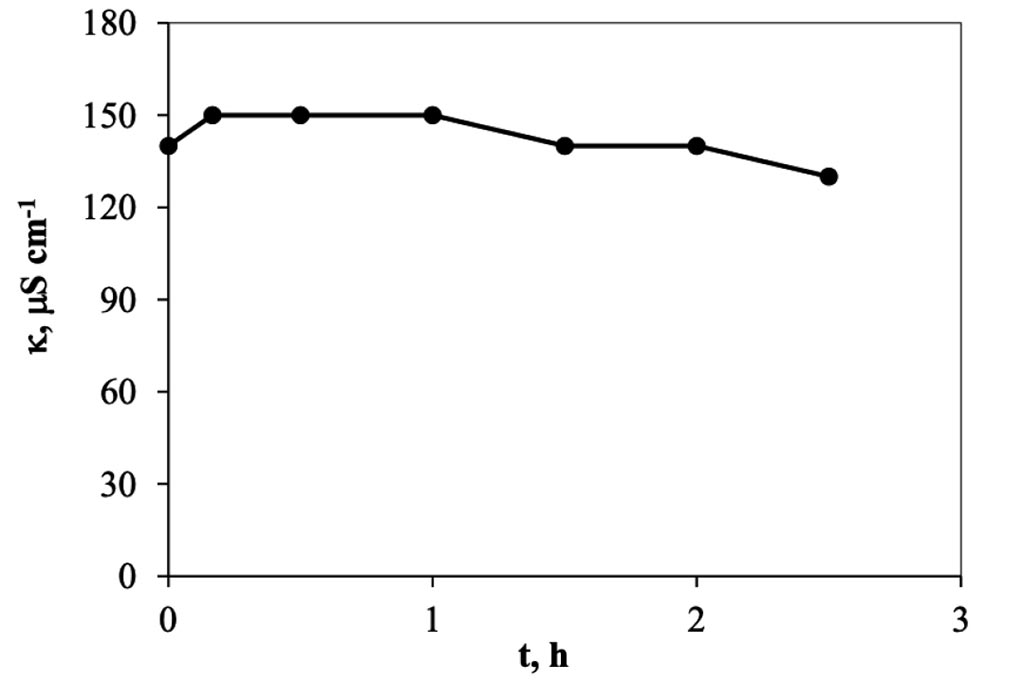
the reversibility of the process and to continue the investigation about new materials in this field. In addition it is recommendable be careful with the pH changes to avoid species precipitation into the system. How could be proved, the pH during electro-sorption was more stable, due to the large volume, in comparison with adsorption process. In addition, although the capacity to electro-adsorb ions is defined per the kind of ion and the surface area, the possibility to do faster the process and to avoid elution or regeneration stage, its attractive to continue the research about new materials, trying to find more physical stability into the electrodes and large surfaces.
Acknowledgments
The present research belongs to Profr. Lucía Alvarado´s group, and it was carried out in the Department of Mine Engineering, Metallurgy and Geology, Engineering Division of the University of Guanajuato´s Laboratories.
References
- C. P. Daniel, M. R. Francisco, Boletín de la Sociedad Geológica Mexicana, 65: 3 (2012) 427-446.
- K. Y. Foo, B. H. Hameed, J. Hazardous Materials, 170 (2009) 552-559.
- L. Alvarado, A. Chen, Electrochim. Acta, 132 (2014) 583-597.
- C. H. Hou, C. Y. Huang, Desalination, 314 (2013) 124-129.
- C. S. Fan, S. Liou, C. H. Hou, Chemosphere, 184 (2017) 924-931.
- A. Ginno, Y. Yoshihara, Energy, 103 (2016) 605-607.
- G. X. Li, P. X. Hou, S. Y. Zhao, C. Liu, H. M. Cheng, Carbon, 101 (2016) 1-8.
- X. Gao, S. Porada, A. Omosebi, K. L. Liu, P. M. Biesheuvel, J. Landon, Water Research, 92 (2016) 275-282.
- R. L. Zornitta, J. J. Lado, M. A. Anderson, L. A. M. Ruotolo, Sep. Purif. Techn. 158 (2016) 39-52.
- J. J. Lado, R. L. Zornitta, F. A. Calvi, M. Martins, M. A. Anderson, F. G. E. Nogueira, L. A. M. Ruotolo, J. Analyt. App. Pyrolysis, 126 (2017) 143-153.
(a) Department of Mine Engineering, Metallurgy and Geology, Division of Engineering, University of Guanajuato, Guanajuato, Mex.
(b) Department of Basic Sciences, Autonomus University of Aguascalientes, Aguascalientes, Mex.