Evaluación del Hydrofloat(TM) para la flotación de partículas gruesas en la Mina Cozamin*
Evaluación del HydrofloatTM para la flotación de partículas gruesas en la Mina Cozamin*
Resumen
Debido a las limitaciones inherentes de las celdas de flotación convencionales, la recuperación es pobre cuando los minerales sulfurosos son más gruesos de 100 a 200 micras. Para abordar esta deficiencia, la División de Flotación de Eriez (EFD) ha desarrollado el HydroFloat™. El HydroFloat es un sistema de flotación de lecho fluidizado diseñado para superar las limitaciones de las celdas de flotación convencionales en la recuperación de partículas gruesas. La tecnología HydroFloat™ ya está bien establecida con más de 50 instalaciones a gran escala en aplicaciones de minerales industriales, tales como el carbón, la potasa y el fosfato. Las pruebas de laboratorio y piloto han demostrado un excelente potencial para la tecnología HydroFloat™ en la recuperación de minerales sulfurosos, incluyendo una demostración a escala piloto de largo plazo en el Copper’s Copperton concentrador de Rio Tinto Kennecott en UTAH, USA.
Se trabajó en conjunto con la mina Cozamin para incorporar el HydroFloat™ en dos puntos de su circuito:
- La inclusión en el circuito de molienda para generar una cola de desecho de mineral grueso sin valor y posiblemente permitir un aumento en la capacidad de la planta.
- Recuperar valores gruesos actualmente perdidos en los jales del circuito de flotación.
Las pruebas se realizaron en el laboratorio de EFD, ubicado en Erie, Pensilvania. Ambas muestras se proyectaron para producir fracciones de tamaño de 700 x 160 µm para ser usadas como alimentación para el HydroFloat. La prueba de HydroFloat de los gruesos del ciclón (bajo flujo) demostró que es posible alcanzar la excepcional recuperación del 95% de cobre en este rango de tamaños. El HydroFloat produjo un concentrado correspondiente al 31% en masa de la alimentación de gruesos y una cola de desecho sin valor que se enviaría como cola final y representa el 69% del total de masa en la fracción de tamaño de 700 x 160 µm, que ya no sería parte de la carga circulante del molino de bolas. Alternativamente, el tratamiento de los jales totales del circuito de flotación actual de Cozamin mostró que con el HydroFloat se puede recuperar el 86% del cobre previamente perdido en la fracción de tamaño de 700 x 160 μm de los jales. En el presente artículo se proporcionan los detalles de los resultados obtenidos.
Estos resultados muestran las extraordinarias posibilidades que puede alcanzar el HydroFloat con el mineral de Cozamin. La posibilidad del proyecto se basa en un análisis económico más detallado que incluya un caso de negocios y un modelo financiero, que indique la mejor ubicación del HydroFloat en el proceso actual de Cozamin.
Abstract
Due to inherent constraints of conventional flotation cells, recoveries of sulphide minerals coarser than 100-200 micron are poor. To address this shortcoming, the Eriez Flotation Division (EFD) has developed the HydroFloat™. The HydroFloat is a fluidized-bed flotation system designed to overcome the limitations of conventional flotation cells for coarse particle recovery. With more than 50 full-scale installations, HydroFloat™ technology is already well established in industrial mineral applications such as the coal, potash and phosphate. Laboratory and pilot-scale testing has shown excellent potential for HydroFloat™ technology in recovering sulphide minerals, including a long-term pilot scale demonstration at Rio Tinto Kennecott Copper’s Copperton concentrator in Utah, USA.
Capstone investigated two ways of incorporating the HydroFloat into their Cozamin flowsheet:
- Inclusion in the grinding circuit to generate a coarse throwaway tail and possibly allow increase of the throughput.
- Recover coarse values currently lost in flotation tailings.
Testing was done at the EFD laboratory facility, located in Erie, Pennsylvania. Both samples were screened to produce 700 x 160 µm size fractions to be used as HydroFloat feed. HydroFloat testing of the ball mill cyclone underflow showed that an exceptional 95% recovery of copper was achievable in this size range. The HydroFloat produced a throwaway tailing, with a mass pull of 31% reporting to the concentrate, and 69% of the mass from the 700 x 160 µm size fraction of the ball mill recirculating load being removed as a barren final tail. Alternatively, treating the Cozamin flotation tailings showed that 86% of copper previously lost in the 700 x 160 µm size fraction of the tailings can be recovered with the HydroFloat. Further details will be provided in the paper.
These results show the remarkable possibilities that can be achieved by the HydroFloat on ore at this plant. Further analysis, including a business case and financial model based on these results should indicate the best location for the addition of the HydroFloat into a brown-field retrofit at Cozamin.
Introducción
La mina Cozamin de Capstone ubicada en Zacatecas, México, es una mina de cobre polimetálico con subproductos de plata, plomo y zinc. Los principales minerales comerciales son la calcopirita (cobre), la esfalerita (zinc) y la galena (plomo). Han estado en funcionamiento desde 2006 y su rendimiento diario de molienda es de 3600 tpd.
Capstone Gold es una empresa innovadora, que abarca la nueva tecnología como una oportunidad para obtener una ventaja competitiva, así como para obtener el mejor resultado de su recurso minero. Recientemente, Cozamin fue uno de los primeros en adoptar el FeedAirJet ™, un sistema de preaireación en línea que puede mejorar el rendimiento de las celdas de flotación (López, 2017). En el presente estudio, Cozamin está evaluando las posibilidades ofrecidas por Eriez con el HydroFloat ™, un dispositivo para la flotación de partículas gruesas, para mejorar la recuperación y posiblemente reducir el consumo de energía y agua.
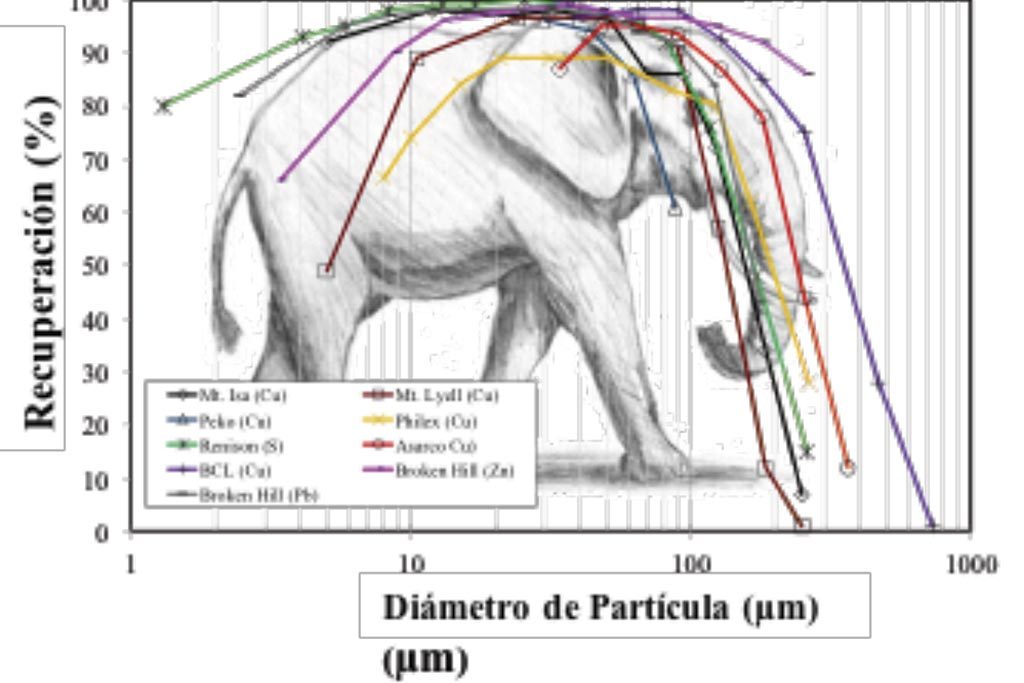
Las limitaciones de las celdas convencionales de flotación son bien conocidas y pueden ilustrarse observando la curva del elefante, mostrada en la Figura 1. Esta curva, que tiene la misma forma para cada sistema de flotación mineral, sugiere un buen desempeño de flotación en el rango medio de tamaños y recuperaciones cada vez más pobres para las desviaciones lejos del centro del rango de tamaños. En el caso de la flotación de partículas finas, un rendimiento pobre se produce por la baja eficacia de contacto y unión de las burbujas y las partículas, mientras que en el caso de la flotación de partículas gruesas, un rendimiento pobre es causado por un mayor desprendimiento de partículas adheridas a las burbujas, así como también por la barrera de altas camas de espuma. Además, el problema de aumentar la densidad de energía específica una celda mecánica para incrementar la probabilidad de contacto entre burbujas y partículas finas, podría causar simultáneamente un mayor desprendimiento de partículas gruesas por la alta turbulencia del medio.
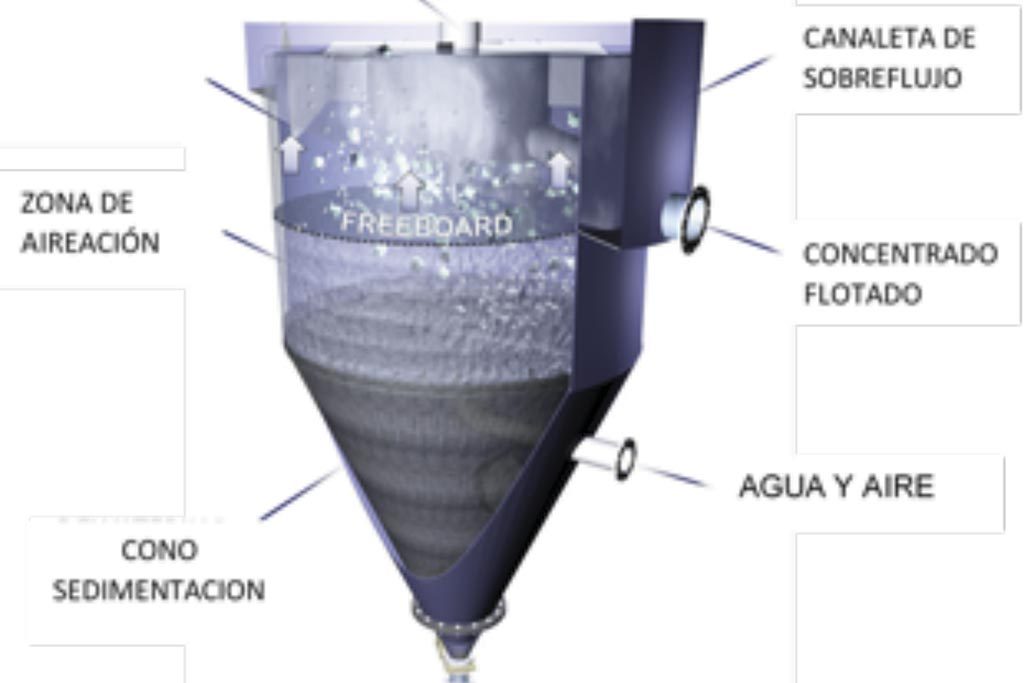
La División de Flotación de Eriez reconoce que el proceso de flotación está controlado por diferentes mecanismos para partículas finas y partículas gruesas. La solución óptima para la flotación es por lo tanto utilizar equipos que han sido optimizados para el rango de tamaño del mineral. En el caso habitual en el que existe una amplia distribución de tamaño, esto significa que la alimentación debe clasificarse de modo que la fracción fina pueda ser flotada usando una tecnología de flotación de partículas finas, como las columnas con inyectores de Eriez tipo Slamjet™ ó CavTube™ (Knoblauch, 2016) o las celdas de flotación de segundo nivel las StackCell™ (Wasmund, 2017), mientras que la fracción gruesa puede ser procesada usando el HydroFloat de Eriez (Mehrfert, 2017). Este artículo presentará un informe sobre un estudio del mineral de Cozamin, procesado por el HydroFloat y ofrecerá dos posibles estrategias para mejorar el rendimiento de la Planta Concentradora utilizando la tecnología de flotación de partículas gruesas, HydroFloat.
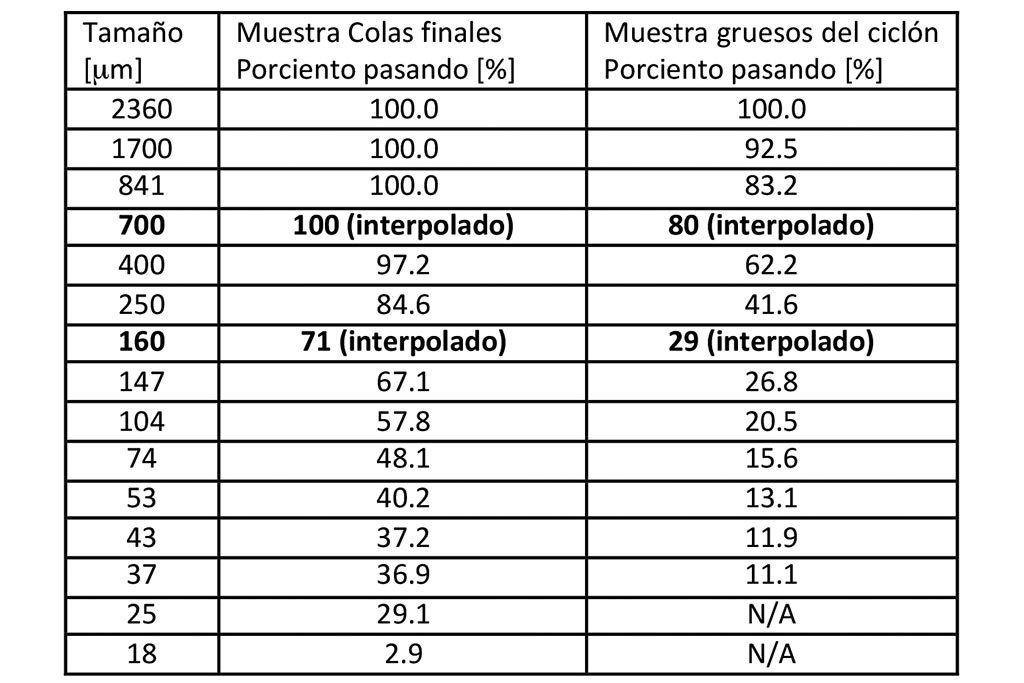
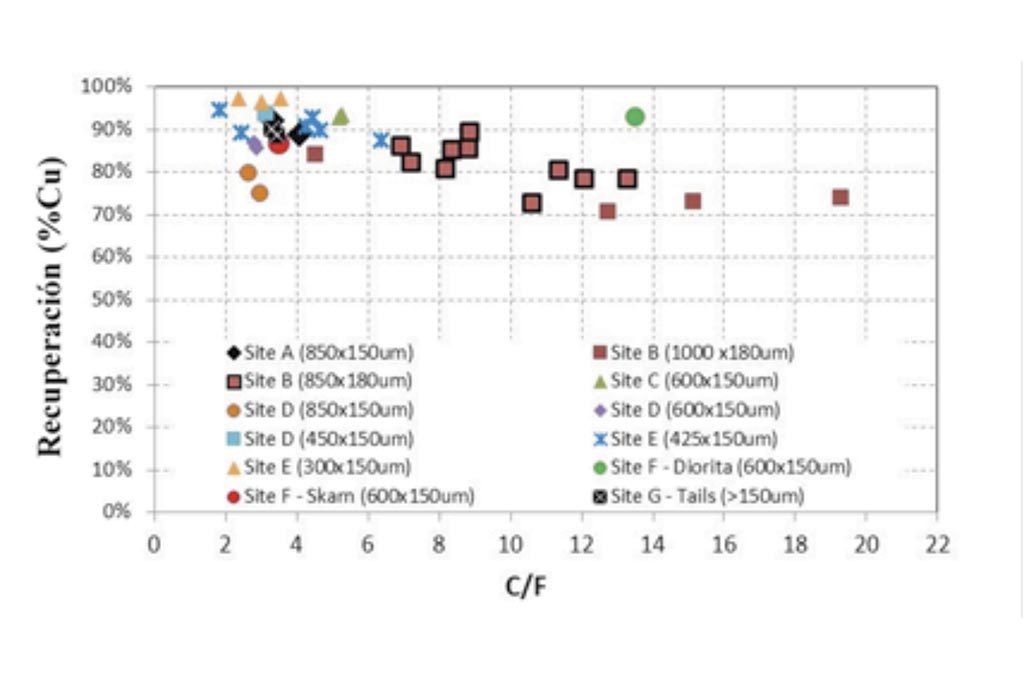
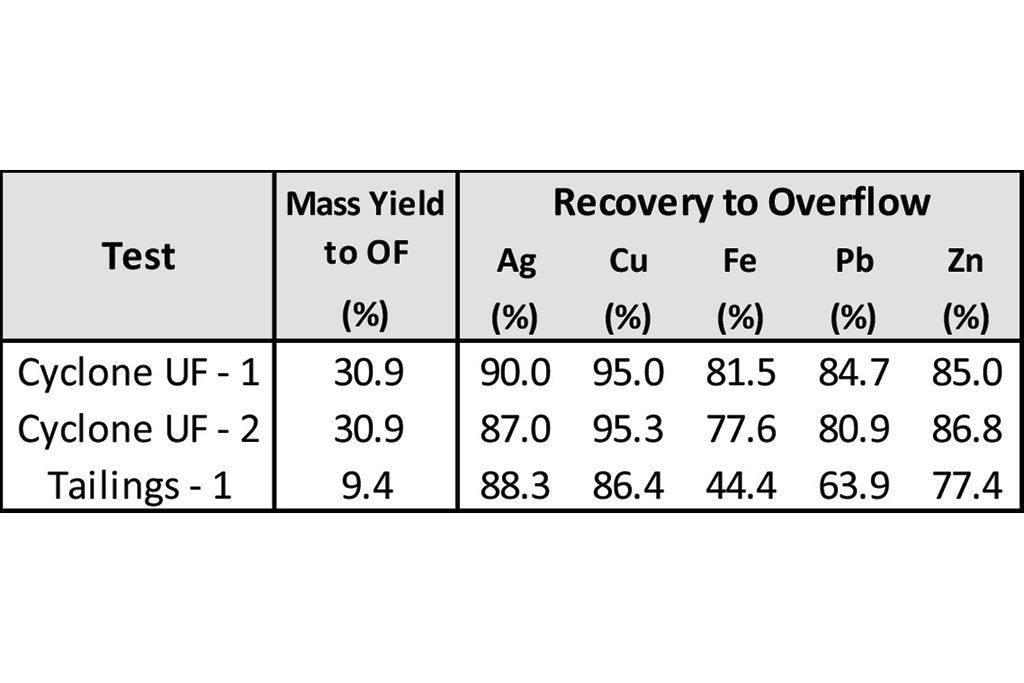
El HydroFloat, fue patentado en 2002 y representa una diferencia significativa con respecto a la flotación convencional. Mientras que la flotación convencional tiene lugar en un tanque mecánico agitado, la flotación de HydroFloat es en un lecho fluidizado con dos fases, una densa en el fondo cónico y una fase de partículas en líquido. En una celda mecánica agitada, se añade energía cinética a través del eje para evitar que la pulpa se sedimente y para crear interacciones burbuja-partícula, manteniendo la turbulencia lo suficientemente baja como para controlar el desprendimiento de partículas de burbujas. Como se ha dicho, este compromiso no funciona bien para las partículas finas y gruesas; no proporciona suficiente energía para flotar eficientemente partículas finas y demasiada energía para flotar eficientemente partículas gruesas. En comparación, el HydroFloat ha sido especialmente diseñado para flotar partículas gruesas con una eficiencia mucho mayor.
Un corte transversal del HydroFloat se muestra en la Figura 2. La alimentación se introduce a través de un pozo de alimentación en la parte superior de la unidad. Un flujo ascendente uniforme de agua aireada crea una fase densa de lecho fluidizado en el que los agregados de partículas y burbujas se empujan a la parte superior del lecho donde continúan contactando burbujas en la interfaz del lecho fluidizado y el freeboard. Después se elevan a través del freeboard y son descargados en la parte superior en una canaleta de concentrados. Un artículo reciente ha mostrado que las partículas gruesas con un nivel de mineralización superficial mínimo de aproximadamente 1% pueden ser flotadas con el HydroFloat (Miller, 2017). La unidad funciona de forma diferente a la flotación convencional en los siguientes aspectos.
- No hay ninguna agitación mecánica dentro de la unidad.
- Un flujo uniforme ascendente de agua de fluidización aireada aumenta la flotabilidad al incrementar la resistencia de las partículas y de los agregados de burbujas con partículas gruesas.
- El contacto de la alimentación y las burbujas es a contracorriente y esencialmente se mejora la mezcla y se reduce el cortocircuito.
- La alta densidad de partículas y burbujas dentro del lecho fluidizado, crea una mejor cinética de flotación (por la ley de acción de masas).
- El flujo dentro del lecho fluidizado es menos turbulento, lo que aumenta la eficiencia del transporte de burbuja-partícula a través de la fase de pulpa.
- La separación de espuma en la parte superior del freeboard se consigue con una profundidad de espuma de “orden cero”, lo que minimiza la caída de las partículas gruesas en la interfaz de borde libre y aire.
La clave de la tecnología HydroFloat es formar un lecho fluidizado estable. Los lechos fluidizados son más estables cuando el rango de tamaños de partículas que componen la cama no son demasiado extremos. Por esta razón la alimentación al HydroFloat es clasificada antes para tener una relación 5:1 del tamaño mayor al menor. Las partículas más pequeñas, debido a su tamaño, se concentrarían en el derrame del producto de flotación, independientemente de si se unen burbujas o no, por lo que el HydroFloat no será selectivo para partículas muy finas. La Figura 3 muestra las curvas grado-recuperación, del HydroFloat, para muestras tomadas de siete sitios mineros diferentes en Perú.
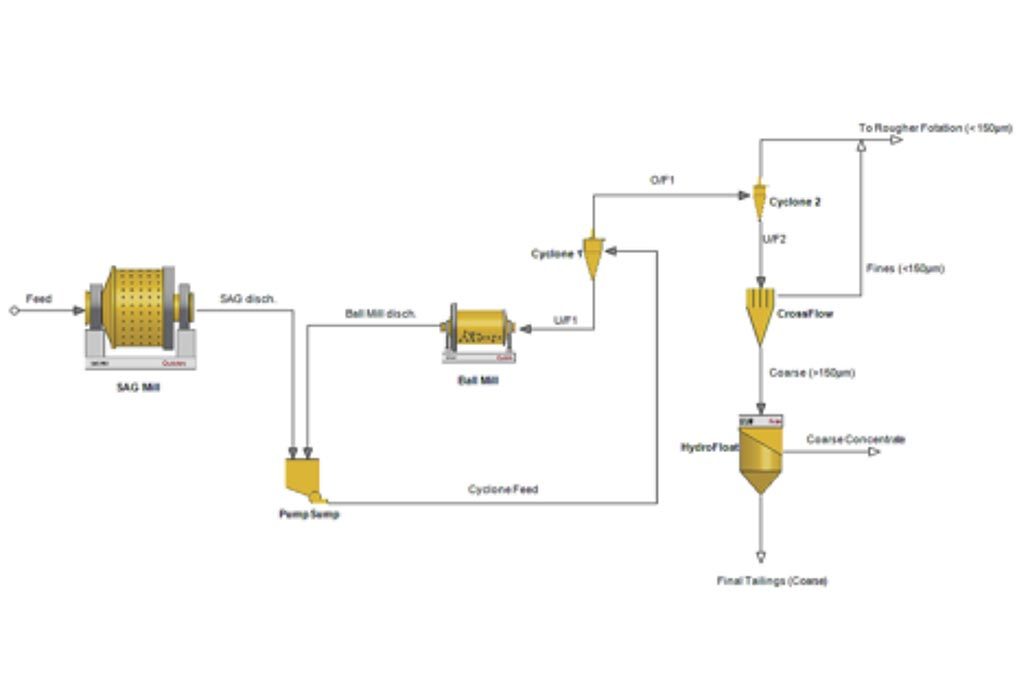
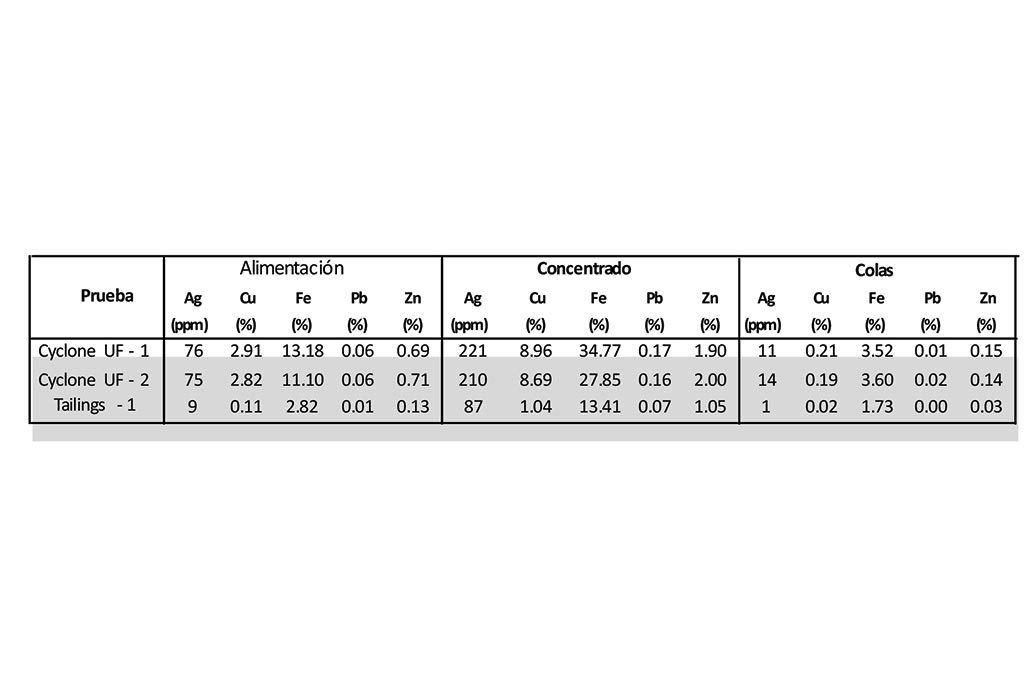
Hay dos posibles ubicaciones donde el HidroFloat puede ser utilizado para mejorar el funcionamiento de los circuitos de flotación existentes. La primera posibilidad es integrar el HydroFloat en el circuito de molienda convencional, por ejemplo en la descarga de sobre tamaño de los ciclones o cribas que típicamente se recircula a la alimentación del molino, como se muestra en la Figura 4. En esta diagrama conceptual, el material muy grueso es removido de la alimentación del HydroFloat con un ciclón secundario y la fracción fina mediante un CrossFlow™, un eficiente hidroclasificador. Esto podría permitir un aumento en el tamaño de molienda permisible, o molinos más pequeños con reducción de potencia (o aumentando la capacidad de la planta con los molinos ya existentes). Además, podría significar la eliminación de jales gruesos sin valor, en una etapa temprana del diagrama de flujo, lo que podría permitir una arena gruesa para la construcción de bordos, así como una menor necesidad de celdas de flotación convencional. Una segunda posibilidad es usar el HydroFloat para recuperar valores de la corriente existente de colas de flotación, como se muestra en la Figura 5. Este enfoque es también prometedor porque los jales en la mayoría de las plantas llevan todavía valores en los extremos finos y gruesos de la distribución de tamaños, siendo una consecuencia de la curva del elefante (Figura 1). Como ejemplo de esto, en la Figura 6, se encuentran las distribuciones de tamaño de dos muestras de jales en las Américas, separados por más de 10.000 km, y cada una de las plantas con capacidad superior a 100.000 toneladas por día. En ambos casos, aproximadamente 80-85% de los metales residuales en las colas se concentraron en la fracción fina y gruesa.
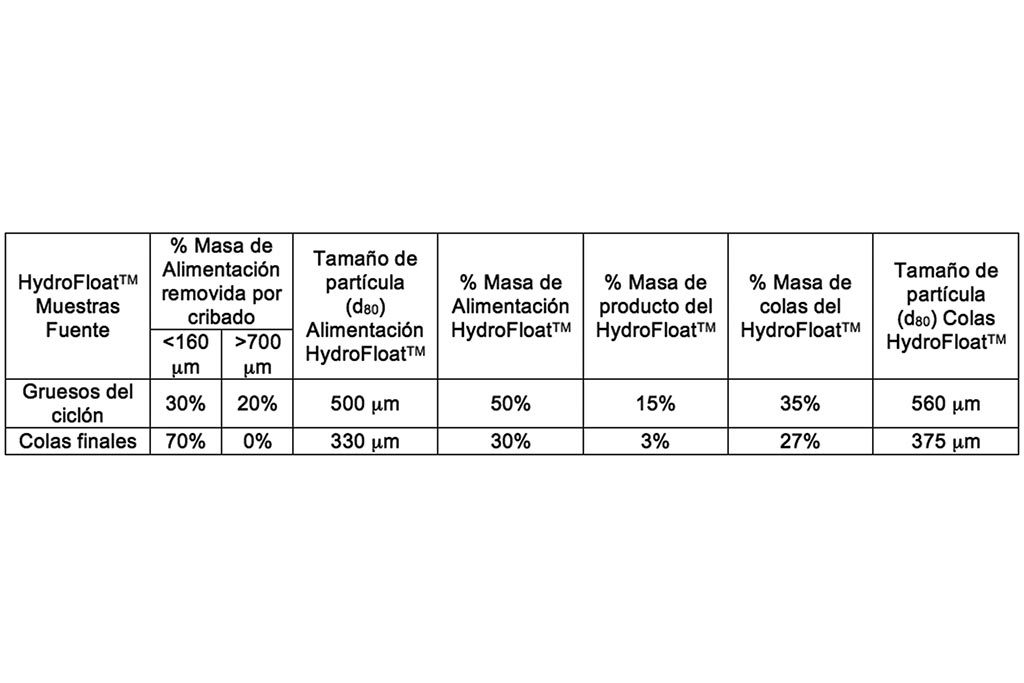
Metodología
En este estudio, el material de la Planta Concentradora de Cozamin fue enviado al laboratorio de pruebas de Eriez en Erie, Pensilvania, USA, para evaluar cada una de las posibilidades discutidas en la sección anterior. Se recibieron aproximadamente 60 kg de los gruesos del ciclón y 20 kg de colas de flotación. Para simular la clasificación de tamaño de 2 etapas (eliminación de gruesos y finos) que se requiere para crear la proporción óptima de tamaño 1:5 para el HydroFloat, las muestras recibidas se clasificaron individualmente a 700 μm y 160 μm utilizando un tamizador vibratorio marca Sweco. Después de la clasificación, aproximadamente 35 kg y 14 kg de material de 700µm x 160µm de los gruesos del ciclón y colas, respectivamente, fueron puestos a disposición para las pruebas del HydroFloat. Las distribuciones aproximadas de tamaños para ambas muestras de Cozamin se muestran en la Tabla 1 y gráficamente como la Figura 8. Interpolando puntos de estas dos distribuciones de tamaños y asumiendo que la segunda etapa de cribado era perfectamente eficiente, podemos calcular que la cantidad de material fuera del intervalo de [160 micras, 700 micras] fue de 50% para la muestra de gruesos del ciclón y 30% para la muestra de colas finales. El 80% por ciento pasando de la distribución de tamaños (d80) para las muestras cribadas de alimentacion al Hydrofloat fue de 500 µm y 330 µm respectivamente, como se muestra en la Tabla 4.
Se utilizó un HydroFloat de 6 pulgadas de diámetro, mostrado en la Figura 7, para la flotación de partículas gruesas de las muestras de colas finales de flotación y gruesos del ciclón. La alimentación de HydroFloat se acondicionó en lotes de 15-20 kg durante 10 minutos en un acondicionador rotatorio utilizando una combinación de 3418A, xantato de etilo y diésel. El Flomin F-663 fue introducido en el HydroFloat por inyección en la línea de agua del equipo para promover la estabilidad de la burbuja.
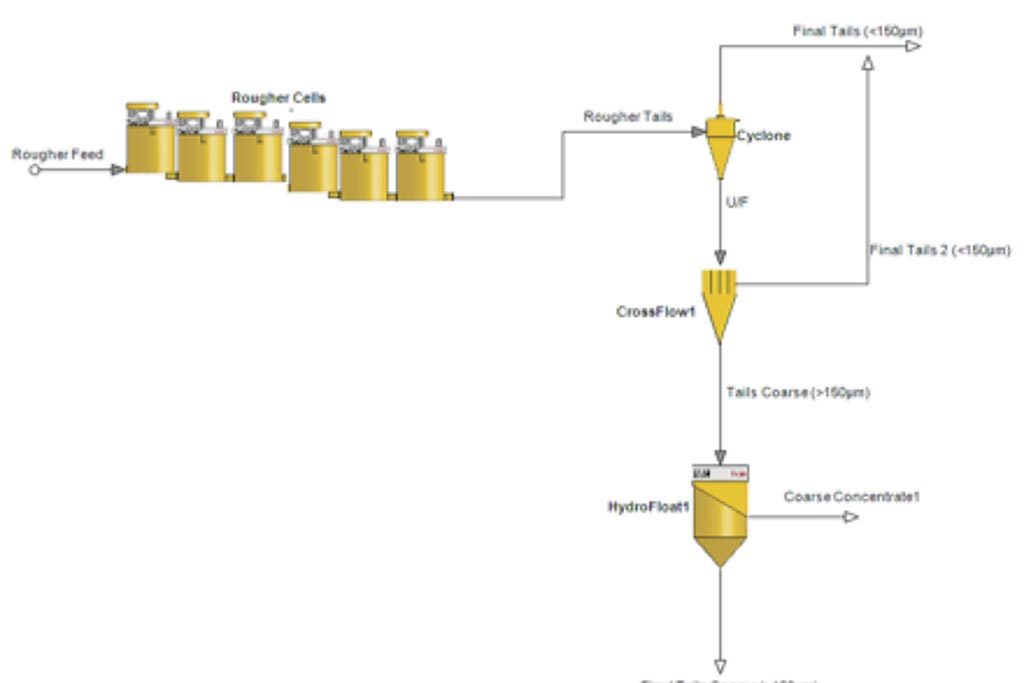
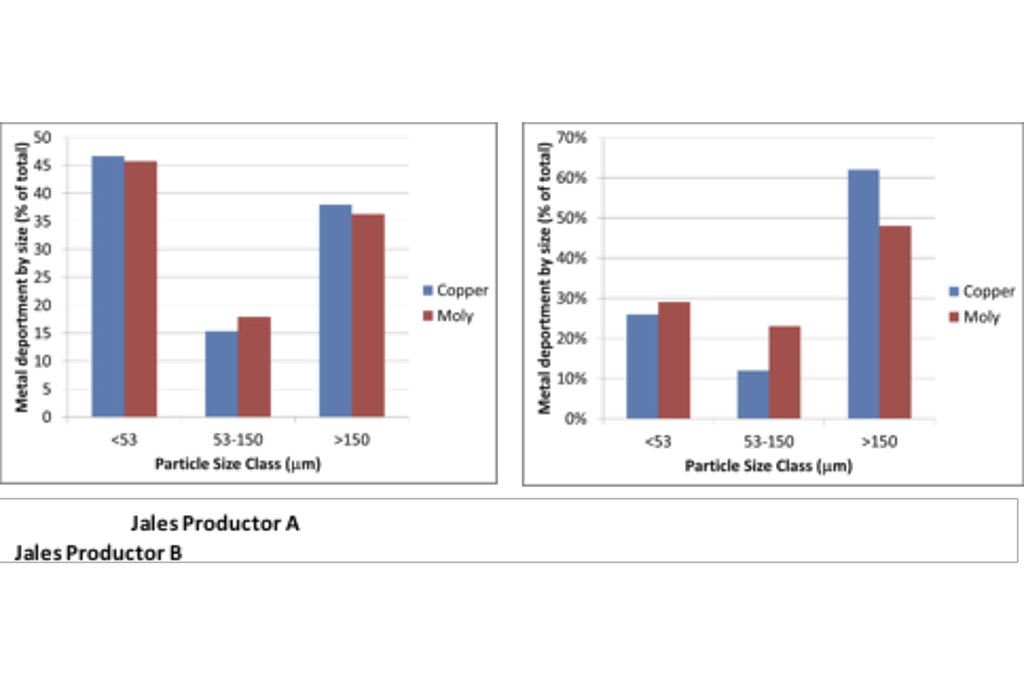
Después del acondicionamiento, la alimentación fue medida en el HydroFloat utilizando un alimentador vibratorio con la adición de agua de reposición para mantener un porcentaje de sólidos que oscile entre 40% y 50% en peso. El ritmo del agua de fluidización del aire y el nivel del lecho fluidizado fueron ajustados para establecer condiciones para cada prueba. Antes de añadir suficiente material de alimentación al HydroFloat, se mantuvo un nivel constante de cama de sólidos usando un controlador automático con un sensor de nivel y una válvula de control de descarga.
Una vez que se alcanzaron las condiciones de estado estacionario en el HydroFloat, se recogieron muestras representativas cronometradas. Se recogió un conjunto de muestras (concentrado en el sobre flujo, colas en el bajo flujo y alimentación) para cada condición de ensayo, con la medida suficiente para el análisis granulométrico. En adición, las pruebas de gruesos del ciclón No. 2 y de colas No.1 fueron analizadas para determinar la recuperación por tamaño. Se usó un ICP-OES para el análisis de cobre, plata, hierro, plomo y zinc. Los balances de masa para cada elemento en cada clase de tamaño fueron reconciliados por un algoritmo iterativo que minimiza la suma de los cuadrados de las desviaciones entre todos los resultados medidos y el balance de masa es optimizado.
Resultados
Se realizaron tres pruebas batch con las muestras de Cozamin en el HydroFloat. Dos pruebas fueron realizadas en la muestra de gruesos del ciclón y una con la muestra de colas de flotación. Cada prueba se realizó utilizando esquemas de reactivos y parámetros operativos únicos. Las pruebas del HydroFloat con alimentación de gruesos del ciclón a un d80 de 560 µm (Tabla 4); produjeron recuperaciones de cobre que estuvieron entre el 95.0 y 95.3%, recuperaciones de plata de 87.0 a 90.0%, recuperaciones de hierro de 77.6 a 81.5%, recuperaciones de plomo de 80.9 a 84.7% y recuperaciones de zinc de 85.0 a 86.8%. Las producciones de concentrado en peso, fue de 30.9% para las pruebas 1 y 2 de los gruesos del ciclón. Las pruebas de HydroFloat con las colas de flotación a un d80 de 375 µm como se muestra en la Tabla 4; produjeron recuperaciones de cobre, plata, hierro, plomo y zinc del 86,4%, 88,3%, 44,4%, 63,9% y 77,4%, respectivamente, con un rendimiento de producción de concentrado del 9.3%. Las recuperaciones y los grados de las pruebas del HydroFloat se muestran en las Tablas 2 y 3, respectivamente.
En una prueba con gruesos del ciclón y una de colas, las muestras fueron clasificadas para permitir balances y recuperaciones por tamaño de cada una de las muestras de alimentación. Los resultados también se muestran gráficamente en las figuras 9 y 10. La prueba 2 de los gruesos del ciclón demostró que es posible obtener una recuperación de cobre de más del 97% en la fracción de tamaño de 425 x 160 µm. la recuperación de cobre sólo disminuyo a 86.7% en la fracción de tamaño de 600 x 425 µm, pero disminuyo drásticamente a 51.1% dentro de la fracción de tamaño de 700 x 600 µm debido a la liberación reducida. Para la prueba 1 de colas se comprobaron recuperaciones del 94.1%, 76.8%, y 44.2% dentro de las fracciones de tamaño de 300 x 160 µm, 425 x 300 µm, y 700 x 425 µm, respectivamente.
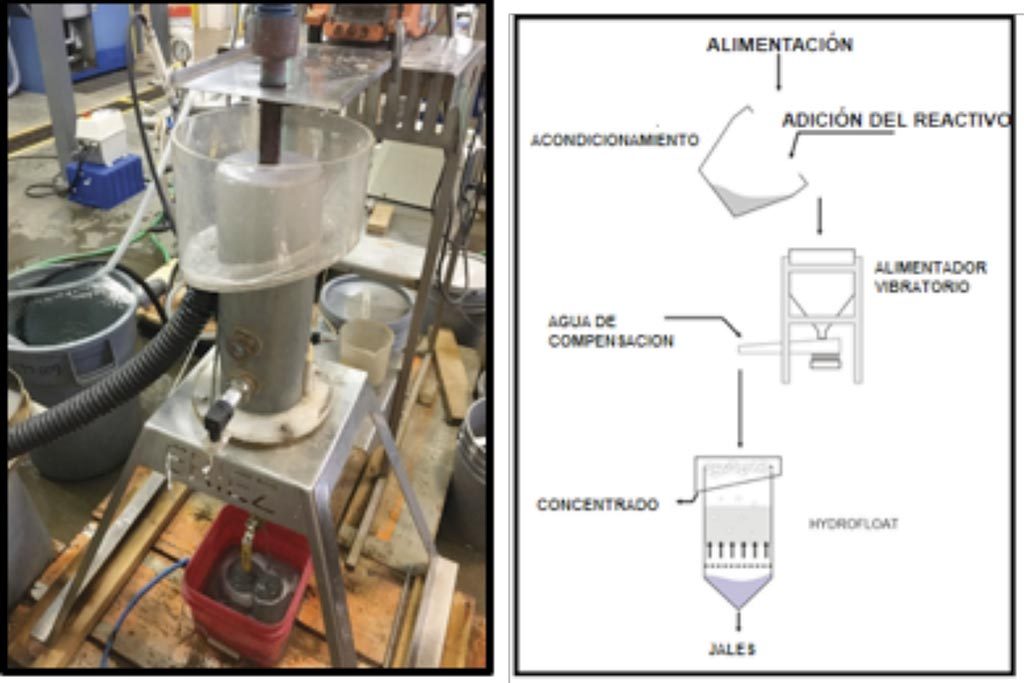
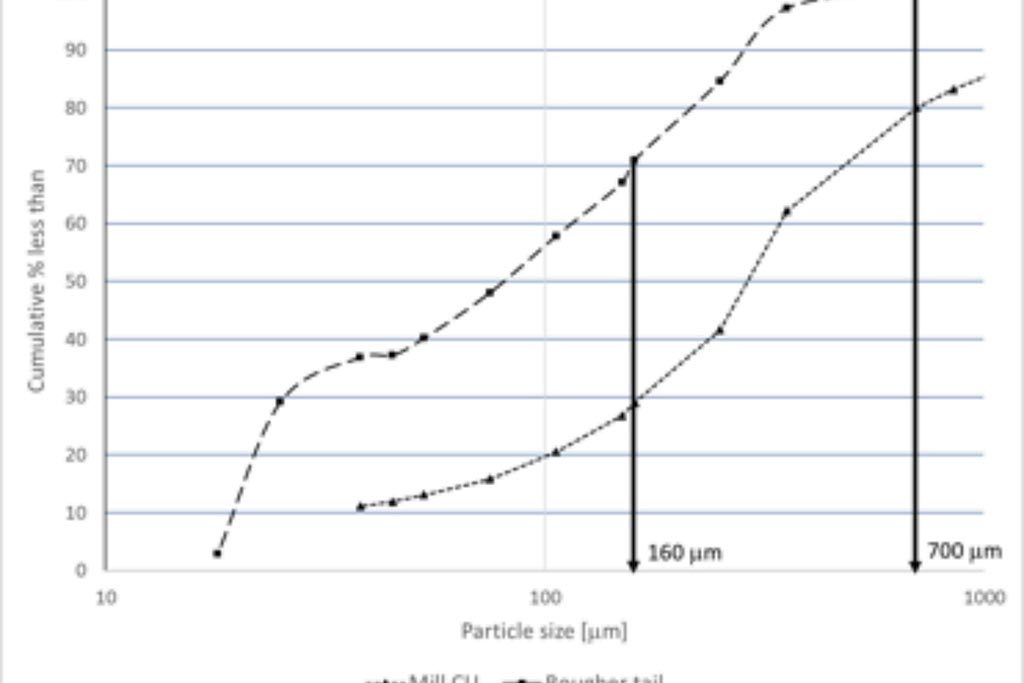
Discusión de resultados
Estos resultados muestran 2 roles potenciales muy interesantes para el HydroFloat en el circuito actual de Cozamin. La primera es recuperar valores de las colas de flotación existentes, como se sugiere en la Figura 5. Los resultados experimentales mostraron que 86% de cobre y 88% de plata en el rango de tamaño [160 micras, 700 micras] de las colas existentes podrían ser extraídas con un rendimiento de masa de menos del 10% usando la tecnología HydroFloat. Esto demuestra la baja eficiencia de la tecnología de celdas mecánicas convencionales para flotar minerales liberados a tamaño grueso y el gran potencial de la tecnología HydroFloat para agotar colas, como se sugiere en la Figura 6. Una variación en este enfoque sería también utilizar la tecnología de flotación fina, como la del StackCell, para recuperar las unidades de metal en la fracción menor de 160 micras de la cola. Eriez cree que agotar las colas será la primera ola de adopción de la tecnología del HydroFloat en el mundo minero, ya que el proceso es independiente del resto del circuito y es relativamente sencillo desarrollar un caso de negocio cuantitativo para la adición de estos equipos.
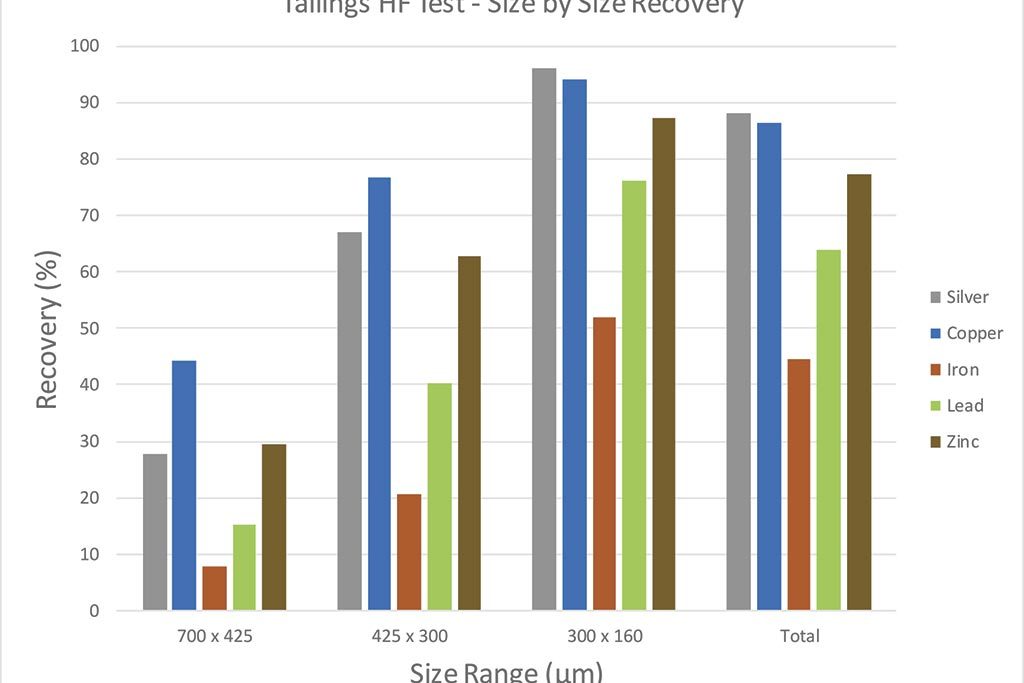
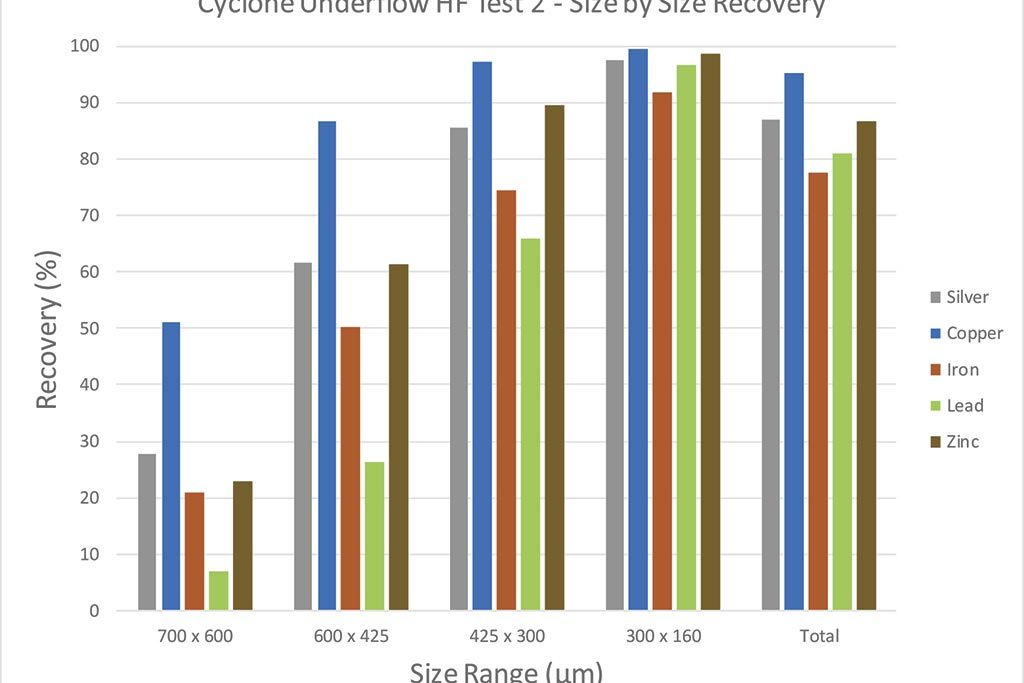
ciclón de Cozamin
Un enfoque más ambicioso sería integrar el HydroFloat directamente en el circuito de molienda como se muestra en la figura 4. Esto permitiría una reducción importante de la masa de material de la carga circulante al molino secundario y en consecuencia, reduce significativamente los requerimientos de molienda capital y costo operativo y crearía una cola de arenas sin valor desechables, que podría ser usada para construir paredes de presa. Además, reduciría enormemente el tamaño de la capacidad de flotación convencional. Con el ejemplo mostrado aquí, los gruesos del ciclón tratados mediante un proceso de clasificación de 2 etapas. Solamente el 20% en masa del material grueso (> 700 micras) tenía que ser eliminado de la alimentación y solamente 30% del material fino (<160 micras), como se muestra en la Figura 8. En teoría, este material grueso excluido (> 700 micras) que es 20% de la producción del molino sería la única parte de la corriente que tendría que ser devuelta al molino, prácticamente ese número seria ligeramente mayor a 20% debido a las ineficiencias inherentes en la clasificación por tamaños. Típicamente, la masa separada que se devuelve al molino a través de la carga circulante es aproximadamente el 70% (para sostener una carga circulante del 300%). La fracción fina, que consta de sólo el 30% de la alimentación de flotación podría enviarse directamente a un circuito primario de celdas de flotación convencionales mucho mas pequeño. Basado en estas pruebas, las colas del HydroFloat, representan el 35% de la masa total que podría ir directo a la presa de jales, así lo confirman los experimentos realizados con el HydroFloat, los valores son los suficientemente bajos como para ser consideradas colas finales (ver Tabla 3), permitiendo un material grueso sin valor con un d80 tamaño de aproximadamente 560 micras para ser removidos del circuito antes de la flotación convencional. Como comparación las colas actuales de esta planta tienen un d80 de aproximadamente 220 micras. Los resultados se muestran en la Tabla 4.
Conclusiones
Estos resultados demuestran los beneficios potenciales para la flotación de partículas gruesas usando el HydroFloat™ de Eriez en dos corrientes de la Planta Concentradora de Capstone Gold en Cozamin. La separación de tamaños de grueso y fino se logró experimentalmente usando cribas, pero se pudo haber logrado en la producción usando ciclones y el CrossFlow™ de Eriez para lograr una alimentación con tamaño para el HydroFloat, de 5:1 en relación de los tamaños superior e inferior.
Los resultados muestran que el HydroFloat podría ser usado en el flujo de colas finales, para recuperar cobre y plata con una recuperación del 86.4% y 88.3%. Esto es posible porque el HydroFloat es muy eficiente para flotar partículas gruesas en comparación con la flotación convencional.
Alternativamente, existe un gran potencial para integrar el HydroFloat en el circuito de molienda convencional. Los resultados mostraron que un proceso de preconcentración con el HydroFloat podría permitir una reducción en la cantidad de material grueso que requiere remolienda de normalmente 60-70% a sólo 20% aproximadamente y una reducción en la cantidad de colas finas y producción de lamas que reduce la capacidad necesaria para la flotación convencional. La recuperación de flotación gruesa para una muestra de tamaño entre 160 y 700 micras fue entre 95.0 y 95.3% para el cobre, 87.0-88.3% para la plata, 77.6 -81.5% para el hierro, 80.9-84.7% para el plomo y 85.0-86.8% para el zinc. Las mejoras potenciales podrían incluir el aumento de la capacidad de la planta, la reducción de la energía en molienda y flotación, el aumento de las recuperaciones globales y la reducción en un 35% del volumen de finos difíciles de almacenar en la presa.
Agradecimientos
Los autores desean agradecer a Mr. Gregg Bush de la oficina corporativa de Capstone Gold y al Gerente de Cozamin el Ing. Abel González por su apoyo en la realización y presentación de este estudio. También se aprecia al equipo de Eriez Wager Road Test Lab en Erie Pensilvania EU, dirigido por Eric Yan y Drew Hobert.
Referencias
- Lopez, O., Improving copper and silver recovery in flotation columns using pre-aeration with the FeedAirJet™: Revista Enlace Minero, 18, p. 14-17, (2017).
- Knoblauch, J., Thanasekaran, H., Wasmund, E., Improved cleaner circuit performance at the DeGrussa Copper Mine with an in situ column sparging system: Proceedings of the CMP2016, p.231-241 (2016).
- Wasmund, E. Rethinking the process: Engineering and Mining Journal, March, p.47-49, (2017).
- Merhfert, P. Investigating the potential of HydroFloat coarse particle flotation: Proceedings of the CMP2017, (2017).
- Miller, J.D., Lin, C.L., Wang, Y., Mankosa, M.J., Kohmuench, J.K., Luttrell, G.H., Significance of exposed grain surface area in coarse particle flotation of low-grade gold ore with the HydroFloat technology, Proceedings of the IMPC 2016, (2016).
* Artículo presentado en la XXXIII Convención Internacional de MInería
1 Cerro de San Roberto S/N Ejido de Hda. Nueva. Morelos, Zacatecas, México C.P. 98100
2 Hacienda La Pila 104 Col Hacienda de Bravo San Luis Potosí, SLP
Email: rsantosmadrid@capstonegold.com.mx